Dedicated to the Finish
Mervyn Jenkins, sales representative for Mirka (UK) Ltd, extolls the virtues of dust-free sanding solutions to help the Irish joinery and furniture industry meet their sustainability objectives.
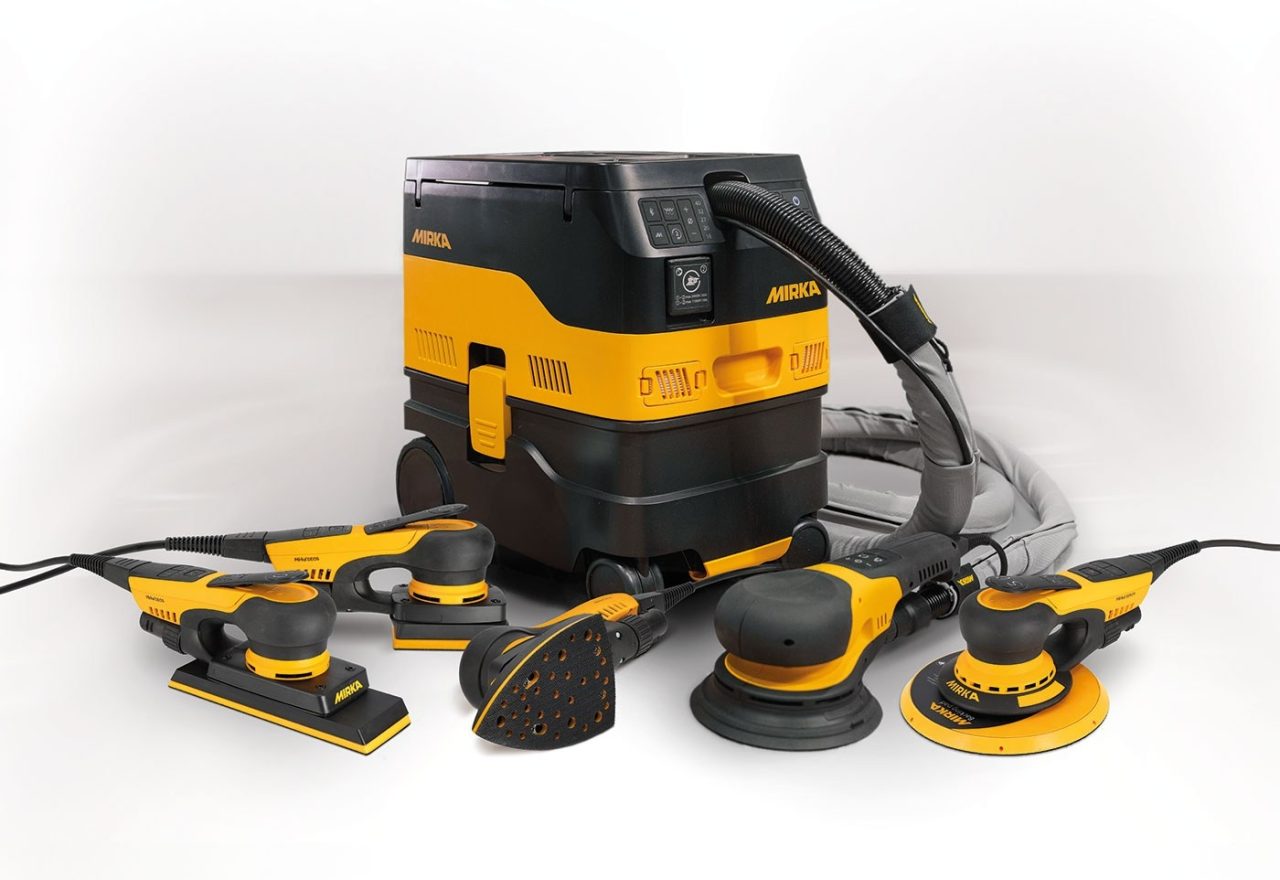
“With one online directory listing showing upwards of 80 large to medium-sized companies within the wood and interiors sector in Ireland, it is safe to say that the Irish joinery and furniture industry is alive and kicking – if not dominating, expanding and excelling against it’s UK based counterparts.
With many family-originated companies entering and surpassing their third decade in business, their experience, confidence and reputations have matured. With the harsh economic winds and wounds of the boom and bust days of the Celtic Tiger at the dawn of the new Millennium far behind, a market sector has emerged which is robust, adaptable, highly skilled and streamlined. In an international dog-eat-dog world of fit-out and design excellence, the growing demand is for providers of on-time and on-budget high-quality interior and exterior manufactured craftsmanship. Ireland is home and a training ground of many such companies.
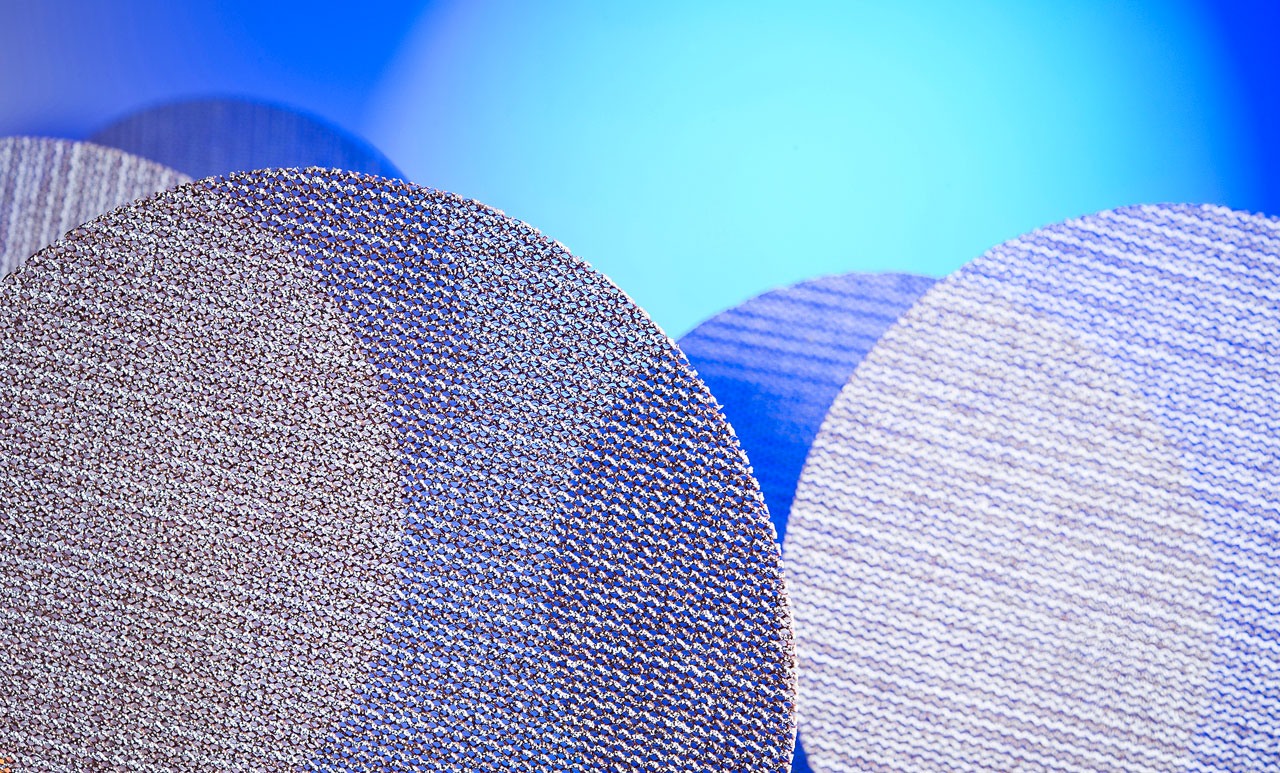
Sustainability drive
In 2025, there are increased pressures for companies to be skilled, capable and competitive as well as sustainable ethical and environmentally responsible. Sustainability, net zero, renewables, and ISOs are the new buzz words infiltrating a sector which has historically been more renowned for turning a blind eye to anything other than the most basic of health and safety requirements.
Since 2015, the Irish Government in tandem with its EU counterparts in Brussels has been pushing for the implementation of ISO 14001 requirements within all business sectors in Ireland. It aims to reduce energy-related greenhouse gas emissions by 50% by 2030.
This has forced many businesses in the furniture and joinery sector to think about their carbon footprint and invest in sustainable manufacturing processes, energy-reducing initiatives and carbon-reducing practices.
With many companies bamboozled by the terminology and overwhelmed by the requirements of the Green New Deal, government organisations such as SEAI – Sustainable Energy Authority of Ireland – have helped educate many about the positive benefits of sustainability.
The furniture and joinery sector has traditionally viewed any form of bureaucracy as a distraction, a necessary evil from the main work of manufacture and profit in an industry squeezed with tight margins and high overheads.
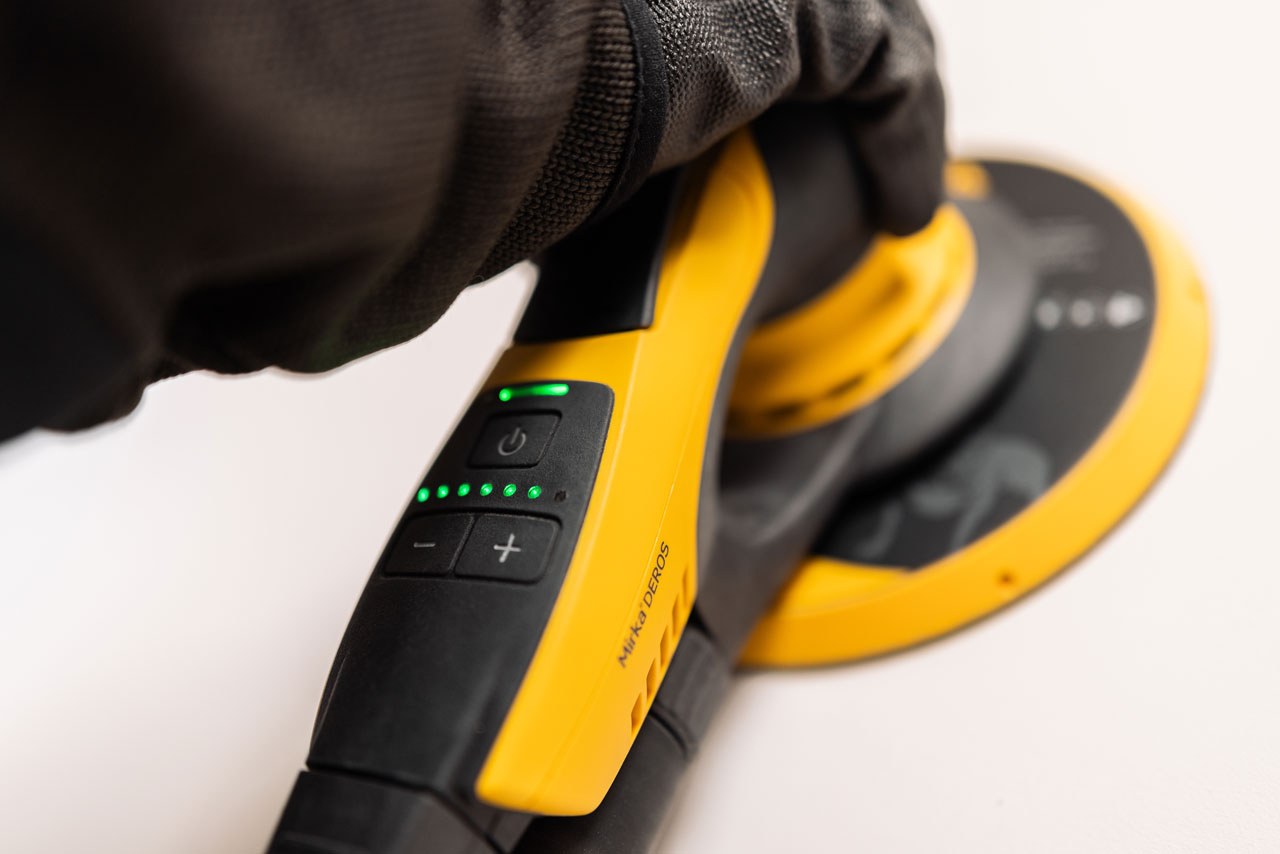
In the last few years, education and explanation have helped many to see the benefits which can be brought to the manufacturing and procurement process and the profitability which comes with a well-planned and ethical approach to all areas of business. Environmental Management Systems (EMS) is the framework by which any organisation may structure and evaluate its environmental processes and progress. In the world of wood and laminates, sanding belts and substrates, the EMS has become just as important to the profitability of the manufacturing process today as the CNC machine became to the production process 20 years ago.
Solar panels, heat pumps, zero landfill waste, LED lights, FSC (Forest Stewardship Council), and HVO biofuel (Hydrated Vegetable Oil) are some of the methods and initiatives helping furniture and joinery companies across Ireland reduce their CO2 emissions.
Jerome Durnin, Continuous Improvement Lead at Farrell Furniture in Ardee, Co. Louth speaking about the company’s decision to move its fleet of company vehicles to HVO biofuel says; “With our nationwide deliveries, we cover a lot of miles, so switching to HVO was an easy choice for our green initiative. It cuts our carbon emissions by 90 per cent and reduces wear on our fleet, with reports of increased fuel efficiency and more miles per tank.”
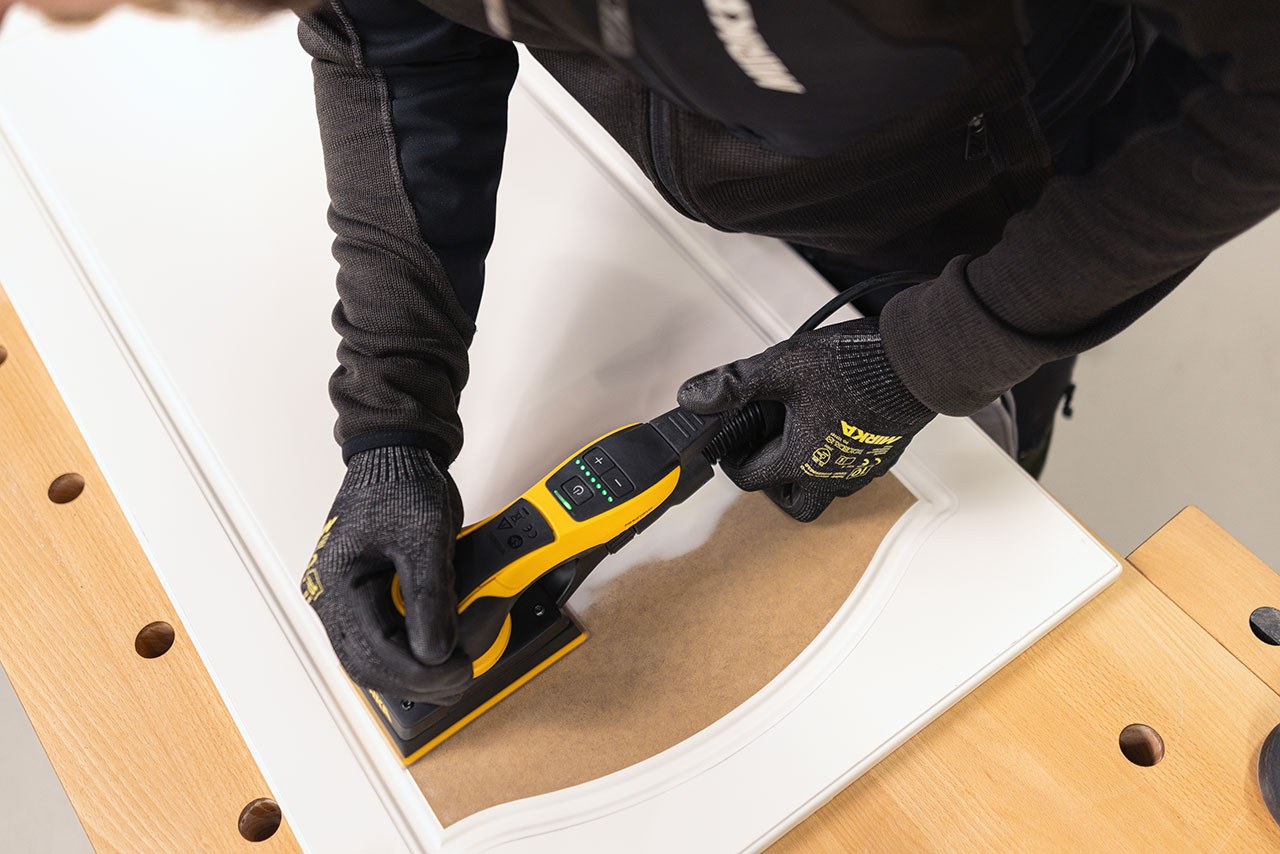
While many of the larger joinery and furniture companies have the money to invest in what must be conceded are relatively expensive initiatives, the downside of the environmental dream is that many smaller companies do not have the same budget or grant options available to them to implement sustainable measures and initiatives to the same extent.
However, the lesson of the ant is a good one to employ for those smaller companies seeking to do their bit in working towards a common goal. Unfortunately, as green a subject as sustainability is, money really doesn’t grow on trees. With subsidies and incentives given to the larger companies which have a quiver full of environmental arrows to shoot alongside their tenders, the smaller companies struggle to win contracts based on the old benchmark of quality, performance and price. They find themselves relegated to sustainability subordinates unable to compete where a sustainability score is the deciding factor in a contract proposal.
Sustainability differentiators aside, the Irish furniture and joinery industry is a well trained, highly skilled powerhouse of talent, ingenuity and professionalism. Fit-out contractors, window and door manufacturers, kitchen manufacturers, chair makers, educational furniture specialists, hotel room furniture specialists, stair manufacturers and railway table makers all manufacture and contribute to the diverse and varied needs of architects, designers and engineers.
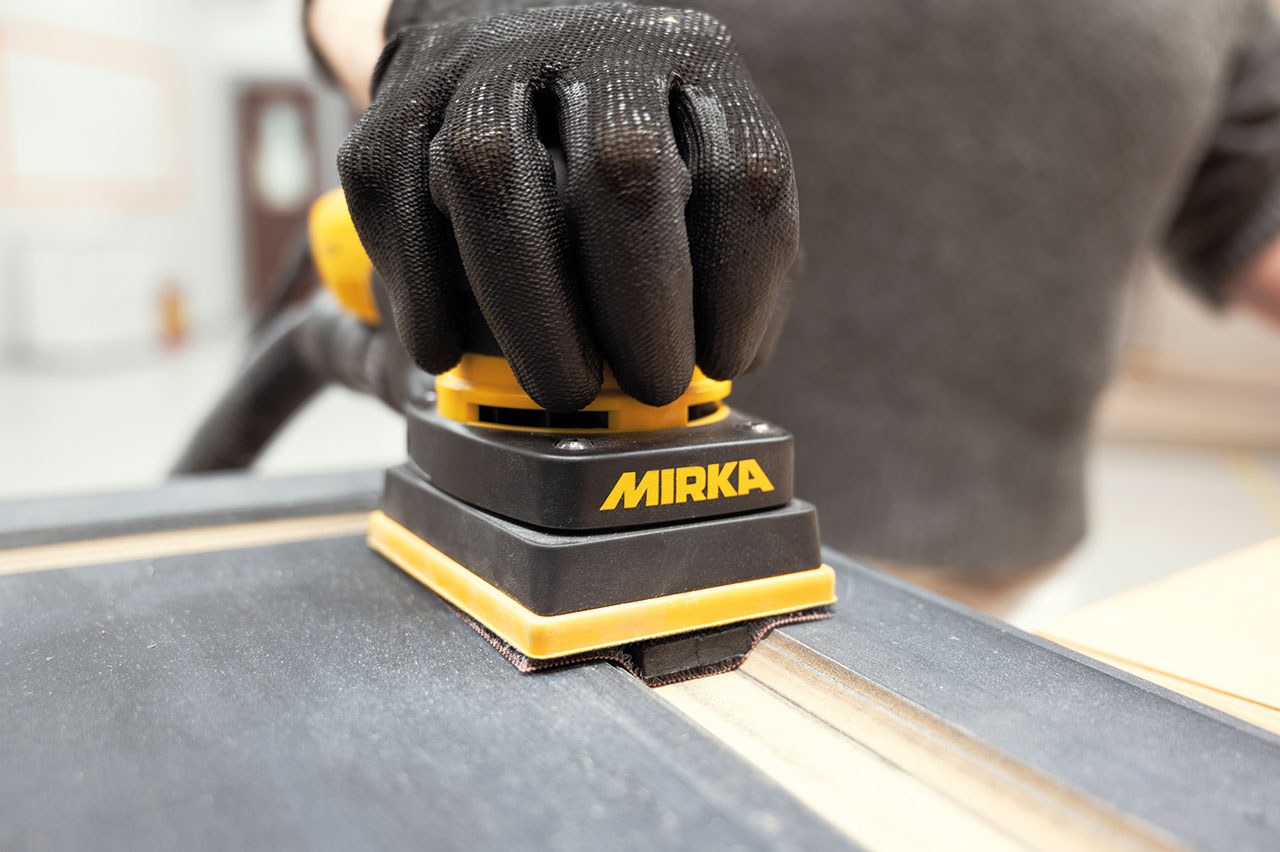
Dust-free pioneer
It is into this domain that Mirka, supported by its local distributors, seeks to make its mark offering dust-free sanding solutions that compliment the sustainability ethos.
Mirka lives, breathes, practices and preaches sustainability, like few other manufacturing companies. Someone once said, “The heart of the matter is the matter of the heart.” If there is a desire for continuous improvement, a desire to find a better way of doing something, and a willingness to adapt, change and learn, then Mirka is a responsible and committed partner, practitioner and helpmate to those on that journey.
Working globally across five different continents and cultures, Mirka recognises the unique challenges and expectations of each individual market sector. The Irish joinery and furniture sector, does not suffer fools and fly-by-night’s gladly. Relationships based on understanding and trust are the cornerstones of successful reciprocal partnerships.
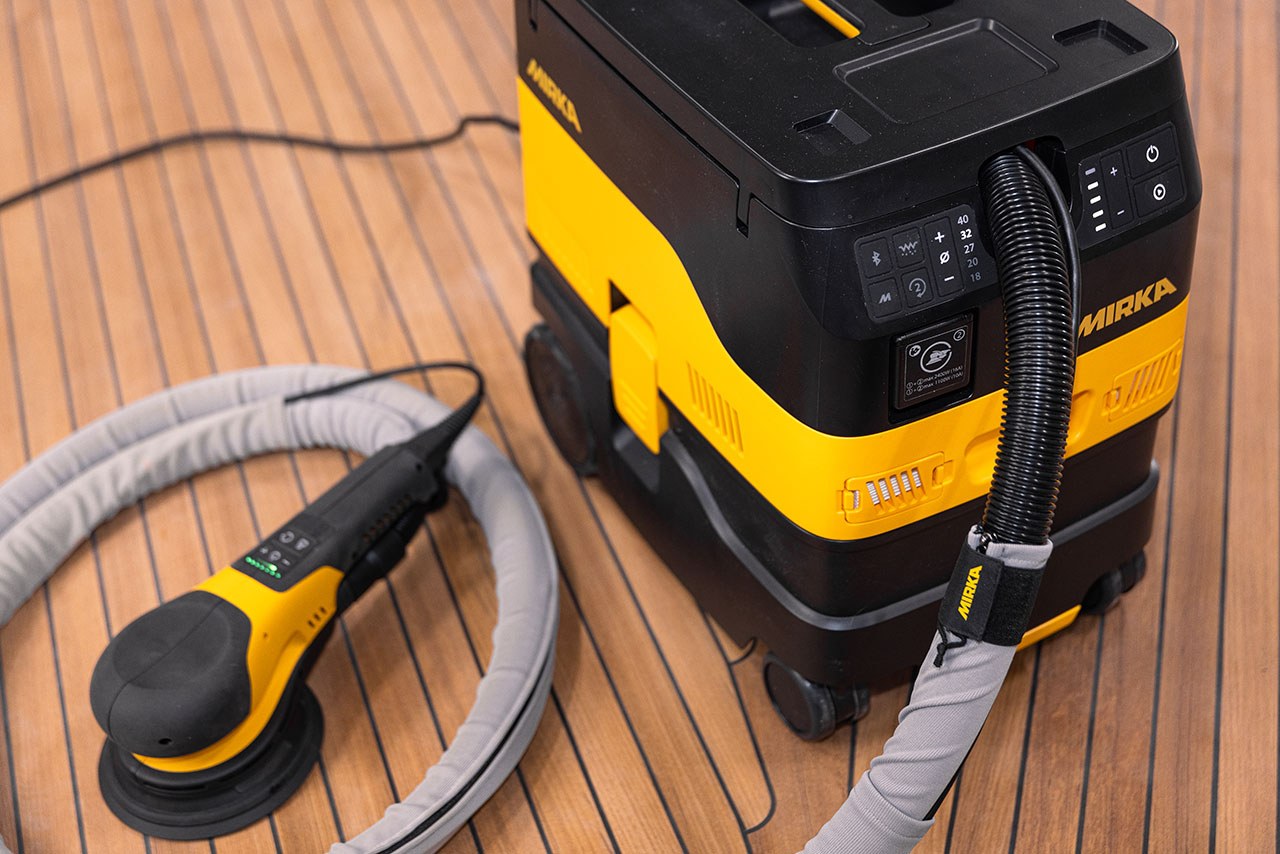
As time consuming as these relationships can often be from the initial prospecting call or customer enquiry, the familiarity of a local Mirka contact who can visit in person and be seen as a trusted advisor is crucial to building long lasting business relationships. The Irish market has long been one in which ingenuity and invention have had a fertile soil.
These factors may account for the keen interest shown in Mirka’s process improvement and time-saving cost reductions. With the technical backup and expertise of 80 years of proven ingenuity and advancement in the sanding and abrasive market, Mirka brings a lot more to the table than those offering impotent innovations and smooth talking.
Innovation
The invention of dust-free sanding, a concept once thought to be confined to the realms of science fiction and human imagination became a reality over 20 years ago with the introduction of Mirka’s truly revolutionary net abrasive Abranet®.
With a patented technology ensuring dust particles were never more than half a millimetre from dust extraction holes, the rules of traditional sanding methods and dust extraction had changed forever. With Abranet being highly resistant to dust clogging on the abrasive surface, not only did the net abrasive remove dust safely, but also this resulted in the cutting performance of the sanding grains staying sharper for longer.
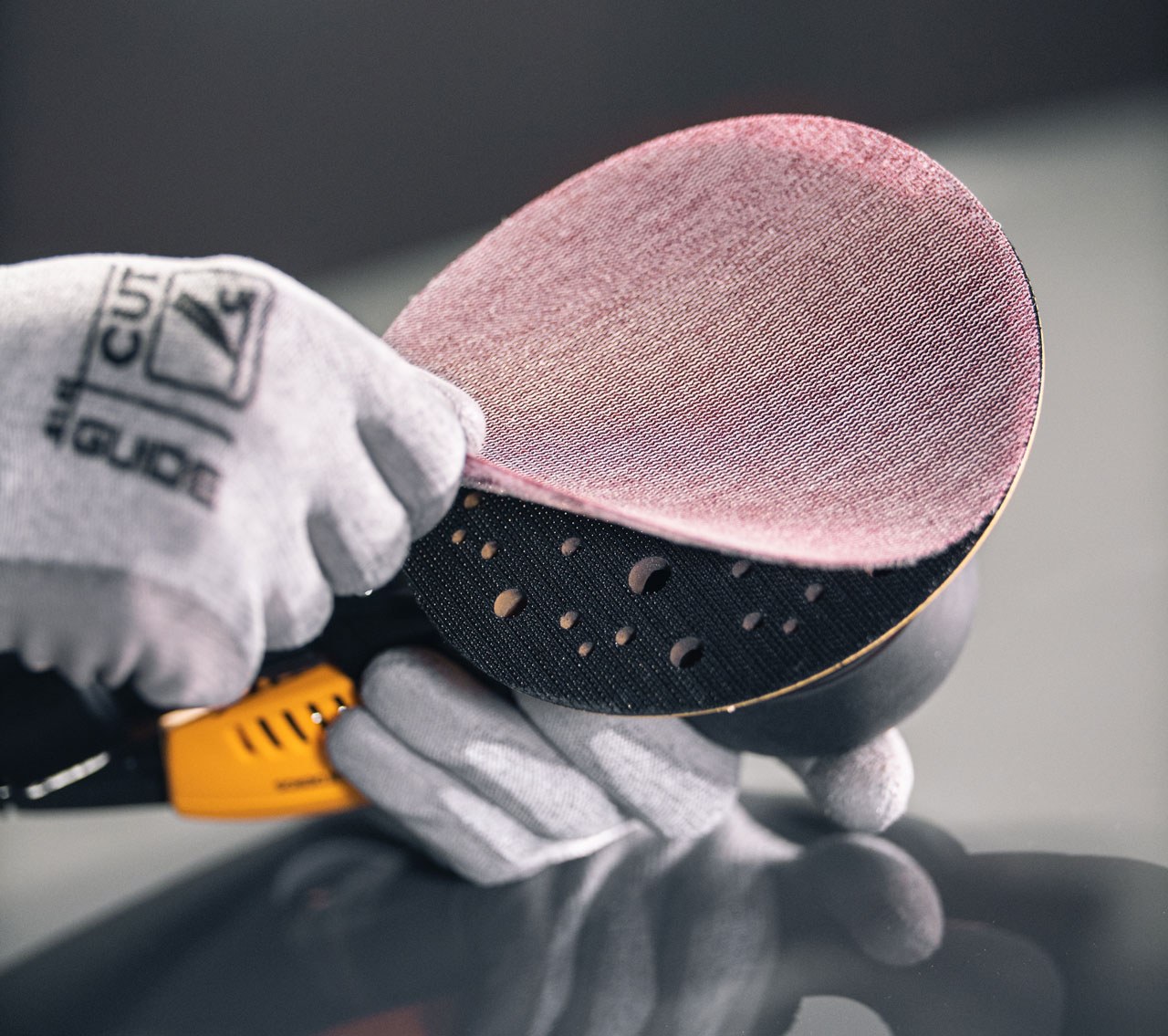
The optimal results of Abranet combined with the power and ergonomics of Mirka’s range of sanding machines and dust extractors have made the evolving and excelling patented product range of Abranet net- abrasives a true game-changer in the field of dust free sanding applications.
For gold-standard flexibility, Mirka’s stearate-coated abrasive paper for dry hand sanding operations is Gold Proflex. It has a highly supple latex-impregnated backing paper that flexes and shapes more effectively to sand contours and profiles as well as flat surfaces effortlessly, producing a consistently smooth finish. Its blue-fired aluminium oxide grain provides a sharper cut and scratch pattern, which removes nibs easily, allowing the abrasive paper to glide over painted or varnished surfaces without rolling, splitting or tearing. Gold Proflex has a resin coat which is well optimised to achieve good aggression, and the anti-slip backing coating also ensures excellent grip and feel.
The stearate coating has been optimised across the grit range to give maximum resistance to clogging and loading, extending the abrasive’s life and maintaining its sharp cut. Available in sheets or rolls, the abrasive comes in grits of 80-400 and has good grit adhesion, allowing the end user to fold the sheet to an optimum size.
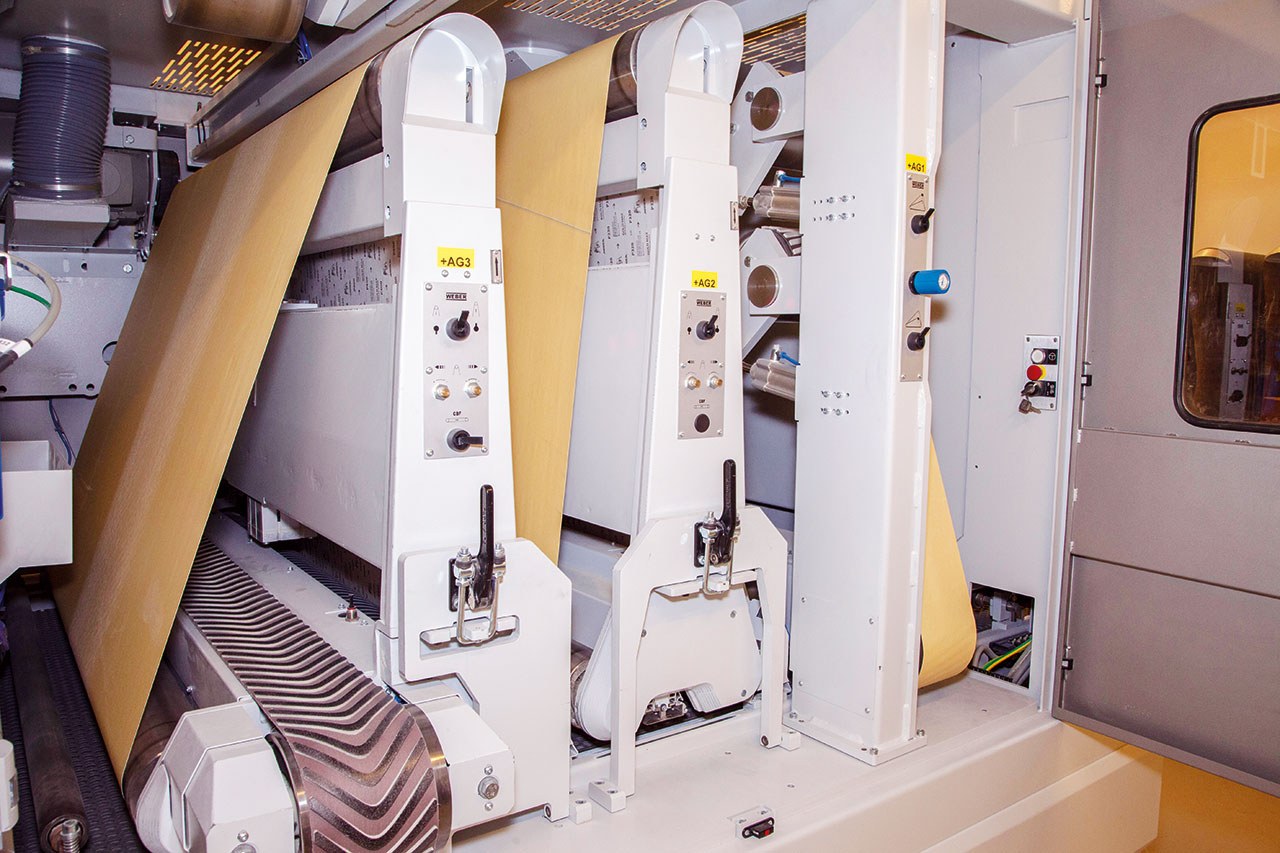
In addition, Mirka’s Gold Max abrasive line-up, specifically for narrow and wide belt sanders, is designed for paint and lacquer sanding. Its stearate coating minimises clogging and pill forming when the abrasive is in use, leading to increased durability of the product and less downtime for the machine. The abrasive’s blue-fired aluminium oxide grains enable it to achieve a high cut rate even on harder paints.
Its innovative anti-static E-paper provides the abrasive with added strength and stability to offer efficient sanding and a smooth surface finish, while the semi-open coating minimises the dust loading on the abrasive so that it can be used on a variety of intermediate and fine sanding applications. Gold Max is available in narrow and wide belts and has a grit range of P240-P800.
To all companies conscientious about quality and professional about their processes, Mirka’s aim is to come alongside as their sanding solutions partner committed to their development respectful of their goals and always; ‘Dedicated to the Finish’.
For further details or to contact Mervyn Jenkins, email [email protected]
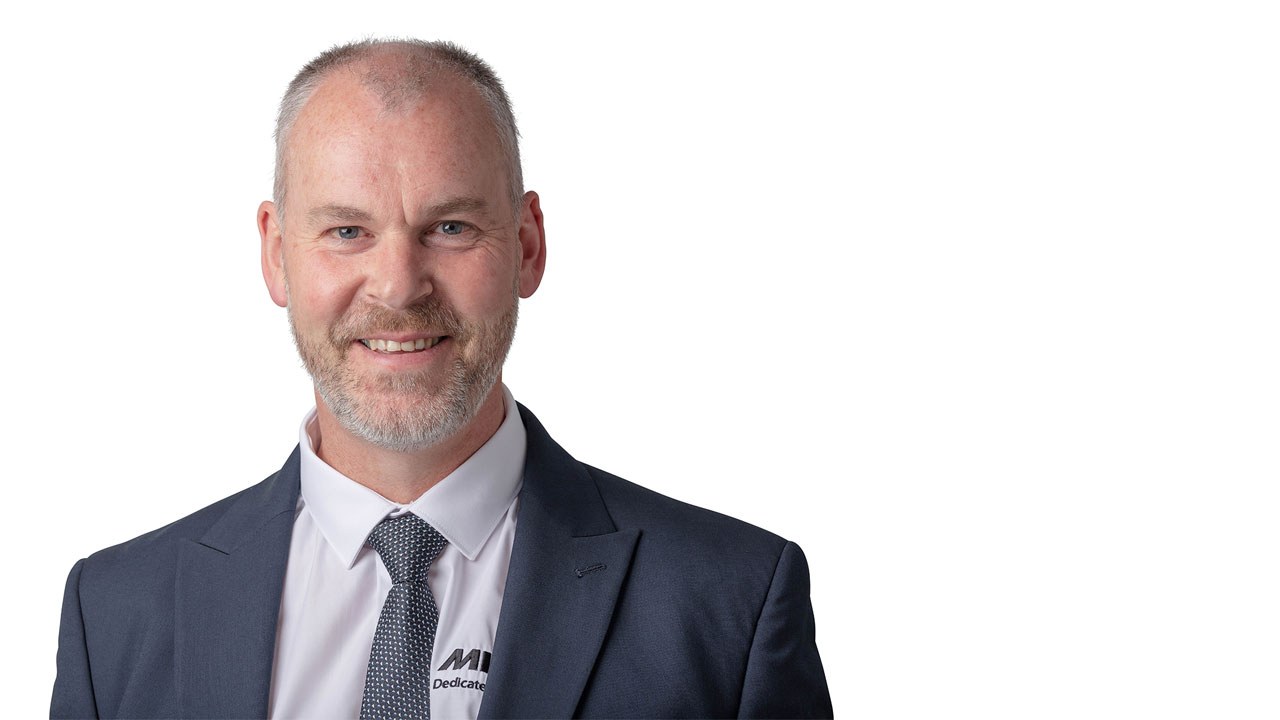